Medical nonwoven fabric is manufactured through a process called "spunbond-meltblown-spunbond" (SMS) or sometimes referred to as "SSMMS" (spunbond-spunbond-meltblown-meltblown-spunbond). This process involves the combination of different layers of materials to create a fabric with desired properties for medical applications.
Here is a general overview of the manufacturing process for medical nonwoven fabric:
Spunbond Layer: The process begins with the creation of a spunbond layer. Spunbonding involves extruding continuous filaments of thermoplastic polymer, such as polypropylene (PP) or polyethylene (PE), and laying them down on a conveyor belt in a random manner. The filaments are then bonded together using heat, pressure, or adhesives to form a strong and uniform layer.
Meltblown Layer: The next step is the addition of a meltblown layer. Meltblowing involves melting a thermoplastic polymer, typically PP, and extruding it through fine nozzles to form microfibers. These microfibers are then rapidly cooled with high-velocity air streams, which cause them to solidify and form a nonwoven web. The meltblown layer provides filtration properties and acts as a barrier against microorganisms.
Optional Additional Meltblown Layers: In certain applications, additional meltblown layers can be added to enhance the fabric's filtration efficiency and protective properties. These layers are created using the same meltblown process mentioned above.
Spunbond Layer (Final): Lastly, another layer of spunbond fabric is added on top of the meltblown layer(s) to provide strength, durability, and a smooth surface finish. The final spunbond layer is bonded to the underlying layers using heat, pressure, or adhesives.
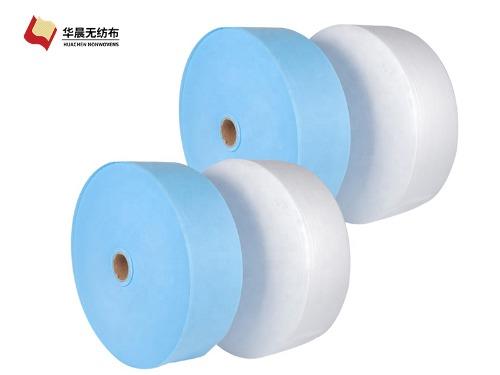
Commonly used materials in the manufacturing of medical nonwoven fabric include:
Polypropylene (PP): It is the most widely used polymer due to its excellent barrier properties, strength, durability, and affordability.
Polyethylene (PE): Another thermoplastic polymer that is sometimes used as an alternative to polypropylene. PE-based nonwovens are typically softer and more flexible.
Polyester (PET): While less common in medical applications, polyester can be used in certain cases where specific properties like higher temperature resistance or improved moisture management are required.
It's worth noting that the composition and construction of medical nonwoven fabric can vary depending on the intended application. Manufacturers may also incorporate additional layers, coatings, or treatments to further enhance specific properties like fluid resistance, breathability, or antistatic properties.